Large medical equipment in the medical profession has to have regular maintenance performed on it in order to assure its usage. The majority of medical professionals have neglected daily maintenance and upkeep of large-scale medical equipment because they have not built a suitable quality management system, which has led to numerous hidden risks of medical mishaps.
In order to do this, it is necessary to improve the quality control of big medical devices, provide effective control prior to, during, and following the event, and conduct a thorough examination of the equipment’s operation procedures in order to ensure appropriate maintenance of the apparatus.
Therefore, under the umbrella of information fusion technology, this study addresses the upkeep, administration, and quality control of major medical equipment. In order to handle the maintenance and quality control of medical equipment, this article outlines the issues that have previously been experienced with its maintenance and develops a medical quality control system. Scientific management theories and techniques are applied in the maintenance system of medical equipment to develop a comprehensive quality monitoring and management system as well as to forecast, adapt, inspect, and account for the quality of the equipment’s whole manufacturing process.
Medical Equipment Maintenance and Quality Control
The major goals of medical equipment maintenance are to increase the device’s useful life, guarantee its integrity and rate of usage, and lower the likelihood that it may malfunction while being used. A new equipment maintenance plan was created by the hospital’s maintenance department based on the features and construction of the equipment to guarantee its functionality and safety. The following techniques, such routine inspections, can be applied to optimise the traditional security measures. Regular instrument repair is also a crucial component of equipment maintenance, as is the daily inspection. Thus, frequent maintenance and ensuring the equipment operates safely are essential to preventing equipment safety incidents.
Adopting international standards
The first step in building a strong quality control system for refurbished medical equipment is adopting international standards. Adherence to international certifications, such ISO 13485 for medical equipment, indicates a dedication to reaching and…
Testing methods
Testing procedures are essential for guaranteeing the performance and safety of medical equipment. Comprehensive analysis and the early identification of any defects in the production process are made possible by sophisticated diagnostic tools and simulation models.
Inspection, fault diagnostics & Testing
Upon arrival at the refurbishing facility, every visible part, mechanical, electrical, transducer, and electronic hardware and software performance are inspected, fault-diagnosed, and tested. Extended Basic tests run after error logs are reviewed.
Refurbishment Proceeds After Inspection & Testing
Depending on which systems require additional testing, which components need to be replaced, and other factors, the process of refurbishment following inspection and testing might vary substantially. For each piece of equipment, then, careful planning and resource allocation are required. When the system was first manufactured and released into the market, the manufacturer registered it as a product, and that registration must apply to the final configuration of the refurbished system. The individuals tasked with organising the essential renovations must possess the appropriate expertise to guarantee that the operations taken will not compromise the authorised configuration or the original identity.
The organisation that does refurbishment must have robust controls for this process step and have it well outlined in its quality management system because of the important nature of the refurbishment planning process.
The actual refurbishment procedure entails the following tasks:
1. Replacing damaged components
2. Cosmetic restoration: painting, surface treatment, and other procedures – System shells are sanitised and repainted after thorough internal and external cleaning, sanding, and rectification of any flaws.
3. Repair of mechanical components: Old and faulty parts are swapped out for brand-new or remanufactured ones that are ensured to adhere to OEM requirements.
4. Repairing electrical components
5. Transducer repair: One of the most crucial components of an ultrasound machine that is being repaired is the transducer. Every ultrasonic transducer is examined for damage to the crystals, bubbles, swelling, and fractures. Cables and connectors are inspected for rips, cracks, and damage. Learn more about frequent ultrasonic probe problems that, if found in time, may be fixed.
6. Repair and replacement of computer systems: Every ultrasonic accessory, including printers, filters, keyboards, and VCRs, is carefully examined and improved to meet OEM requirements.
7. Reassembling the entire system
8. Optional hardware upgrades combined with software updates
9. Comprehensive system, subsystem, and component level quality testing and recalibration – The machines undergo comprehensive testing and calibration, which includes an exhaustive electrical safety inspection prior to a last review of the error logs. The filter service metres are reset and all faults are cleared. Every system is pre-staged and functionally tested in each unit before being sent when the refurbishment procedure is finished.
10.Update Device History Record: In a quality refurbishment facility, the Device History Record (DHR) is updated on a regular basis during the refurbishment process.
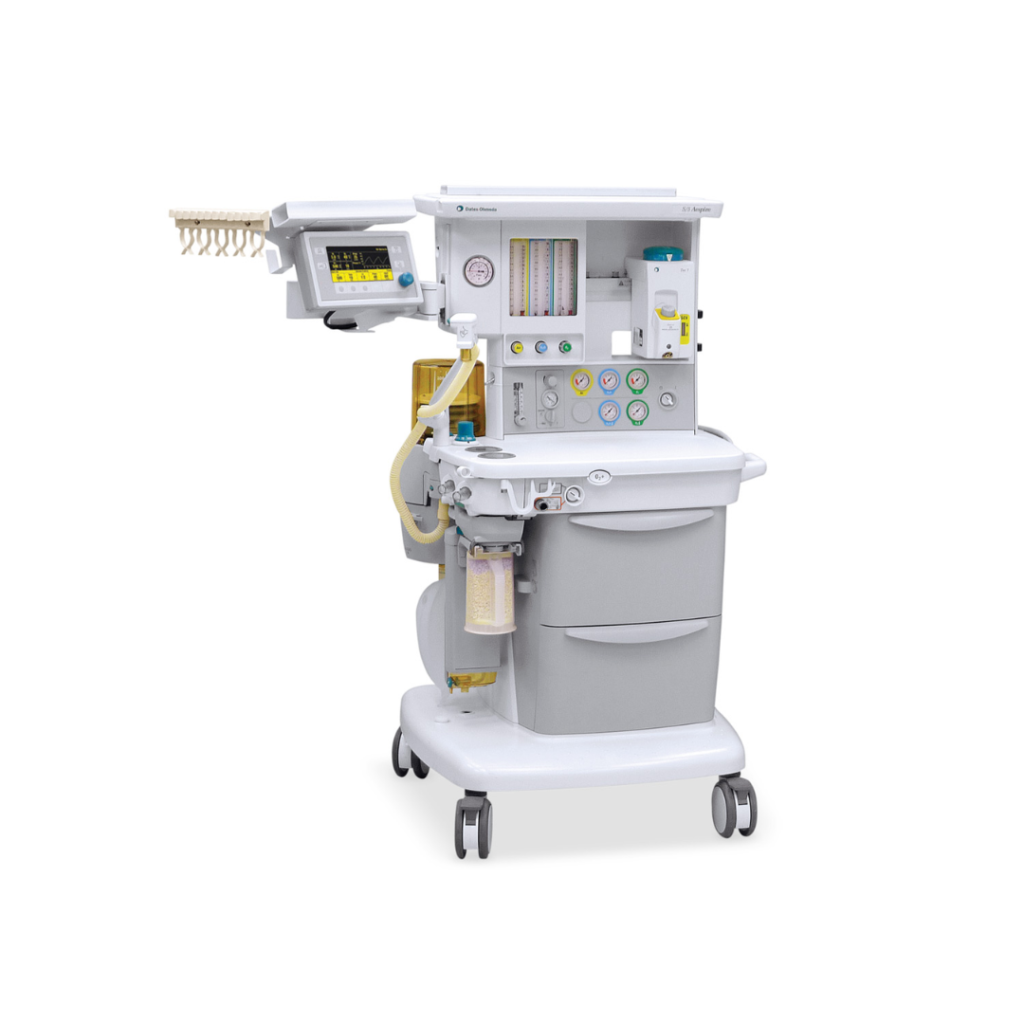
unifiedinc.in
Transforming healthcare with refurbished critical care equipment.